Behind belts drive wheel, after fitting seal, give the seating
a punch to prevent seal from rotating and leaking.
Shims behind flywheel often slids outta place, be thorough.
And do not forget Oring under cyl barrels...
thank you! good advice there! keep it coming!
Waiting for the engine spares at the moment, so filled some time doing some bead blasting on bits and pieces… one of the best bits of kit I have is a blast cabinet… It used to live outside at the back of the garage because I could never seal it from escaping media as obviously the air tries to inflate the cabinet… with machines about abrasive dust is a no no… Then I hit on the idea of a centrifugal type filter, which offers no resistance to the air going through it. I made the filter out of an Ikea plastic box and some sink drain pipe, it vents outside…. the principle is as the air is made to twist and turn, the partials of dust and media centrifuge out and drop to the bottom of the chambers… so the first chamber gets the most, the second less and so on. there is hardly anything on the drive and nothing in the workshop. its difficult to get this level of restoration to a part without it… Bead also gives that nice sheen to alloy parts and they don’t pick up dirty finger prints. its very good at resisting oxidation as well, particularly with a coat of ACF-50… here is the fuel tap.
I used to make a BIG mistake with bead blasting… I could never get a really nice finish except with brand new media… I moaned at the supplier once and he asked me what pressure I blasted at… high as I can I told him.. there is your problem then! you are shattering the glass beads and turning them into sharp dust, hence you get a dull surface! So I went home, filled my cabinet with new bead and got my wife to turn up the pressure as I cleaned a part… soon as it went shiny, that was the best pressure!
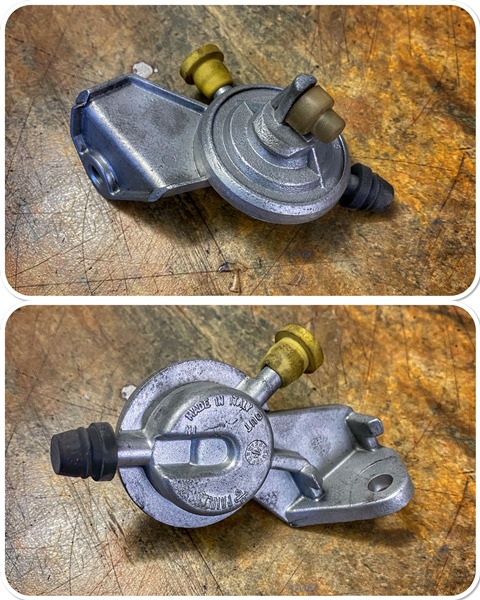
here is the difference old bead high pressure, new bead low pressure!
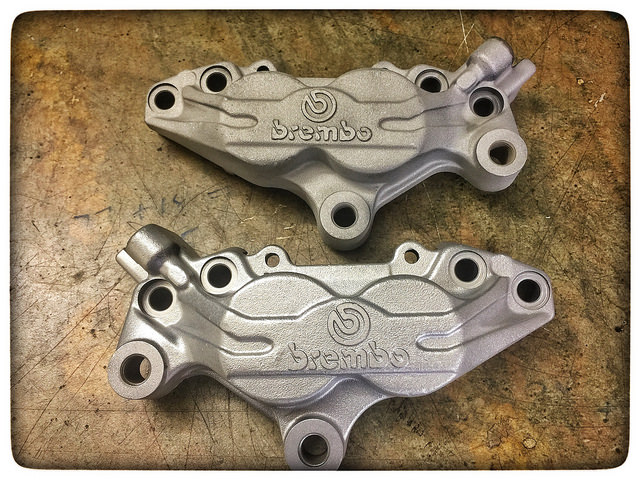
here is a before and after on some weber carbs I rebuilt...
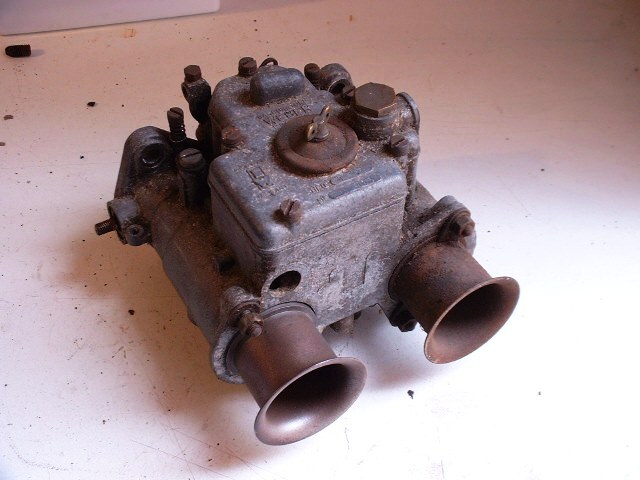
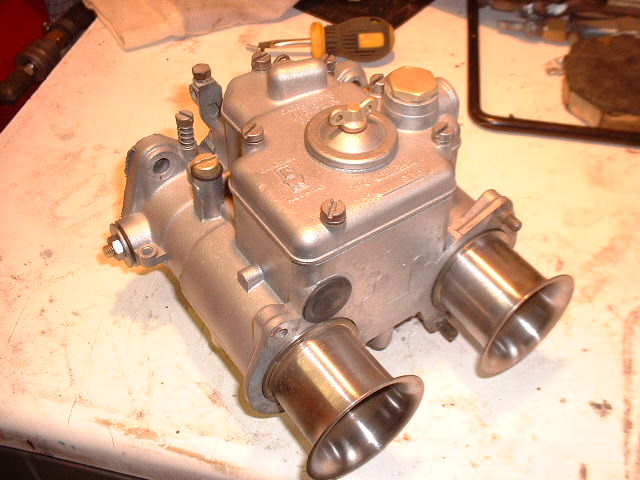
here is how the filter works
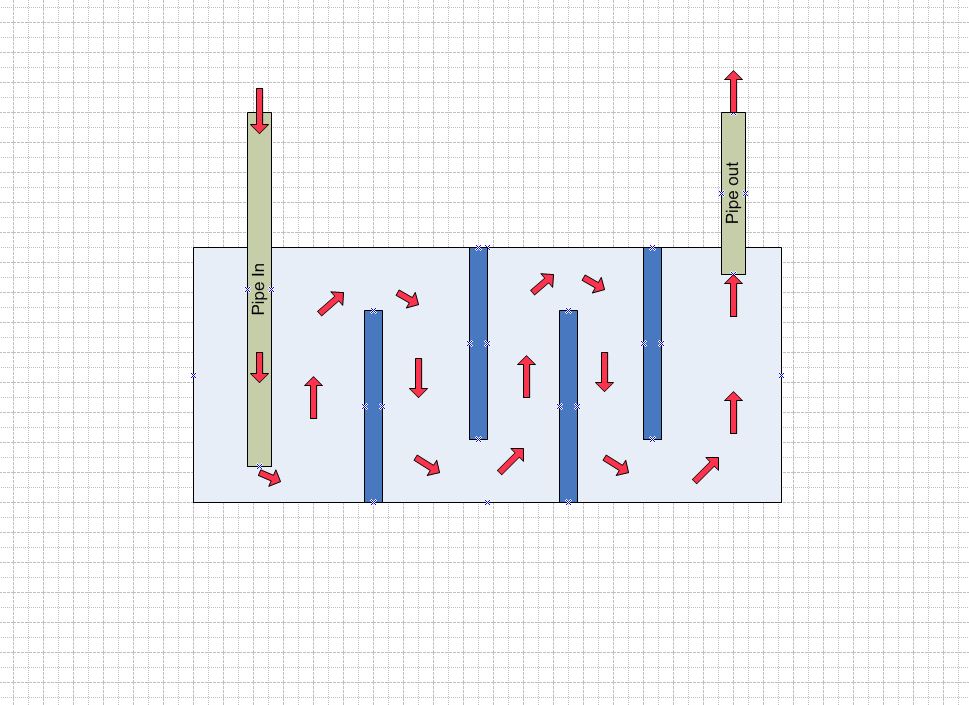