Thanks for you kind words guys, I think Ducati should have released a model with these wheels.
FRONT WHEELThis is the easy bit, just grab a SC 1000 axle and spacer, remove your original wheel and install SC 1000 wheel with matching spacer & axle.
Brakes we'll discuss at a later date.
HUB MODS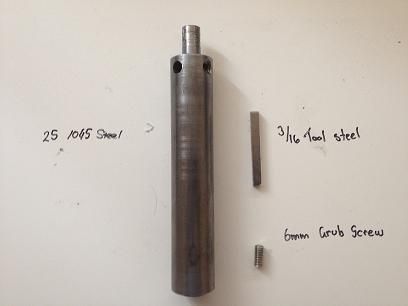
Brake down of the tool, end has been turned down to fit in cordless drill.
5mm drilled and tapped to take M6x1.0 grub screw, metric is more common in Oz.
Suitable hole drilled to take a 3/16 square HSS Tool bit

Just a shot of the assembled tool.
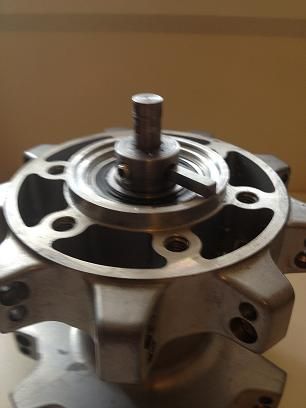
Tool in place to make first cut, not shown arer the packer washers I used between the bearing and HHS bit to set the height.
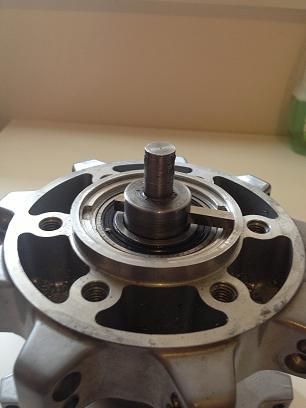
Tool in place for second cut. Once again washers not shown
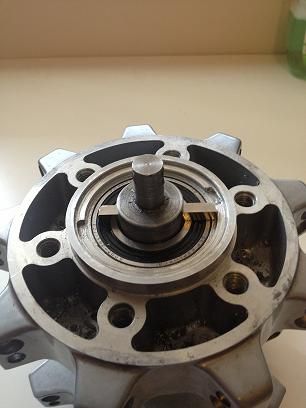
Tool in place for last cut, no washers required as bearing sets bottom depth.
The steel I used was a grade known as 1045 locally. The diameter is a nice fit in the bearings and this holds everything in line.
The tool is chucked in a cordless drill and the cut is made at a speed that gets you a nice cut, a bit of cutting fluid helps in along the way.
The diameters were set by placing the tool in the cast hub and setting the diameter to just a tad under then when at the correct depth a finishing cut is made.
The cut outs for the drive washer were cut with a carbide bit in a dremel tool mounted in a router base, this was cut freehand after tracing the drive washer.
I had a spare hub in the shed to practice on just in case I f*#cked it up. Actually I found this way alot simpler than trying to mount the whole thing on my mill, which would not have fitted anyways. I can't claim this to be an original idea as I poached it from a forum member of aussiestreetfighters. He used the same idea to mod a swingarm pivot on an ally frame. I better add that the method I described requires no unlacing and relacing of the wheel. I wont supply any measurements as I just cut & trimmed to fit.
The speedo drive needed 9mm trimmed off it to fit, a little of the top and most from the bottom. The hardest part was trimming down the white ring gear, eventually I worked out the dremel was the way to go. So far I've put over 2500kays on it and have had no trouble.
One thing I forgot is that there isn't enough space to use the oil seal as per the M900 speedo setup. This will require a little extra care for the speedo drive and maybe the bearings may need replacement earlier. But as usual in these cases nothing is always 100% perfect.